What is Dynamic Positioning?
Qasim Masood AFNI, Head of Qualifications Marine and Offshore at The Nautical Institute, looks at the technology behind Dynamic Positioning and explores the seven components that allows it to function.
Dynamic Positioning (DP) is the art and science of keeping a vessel in a particular position or moving in a particular direction at a particular speed and a particular rate of turn with the help of the thrust generated by its own thrusters. The technology was first developed for scientific research and geological surveys in the 1960s, and was rapidly taken up by the offshore oil and gas industry. Today, it is used in many different sectors of the maritime industry around the world. It offers a wide range of opportunities for seafarers who can gain the necessary qualifications.
Although the DP system itself is controlled by a computer, that does not mean that there is nothing for the operator to do. On the contrary – the operator plays a vital role in managing safety, and has to be able to step in if the system fails. This is a safety-critical role that needs special training. That training starts with understanding the basics of what the system is doing and why.
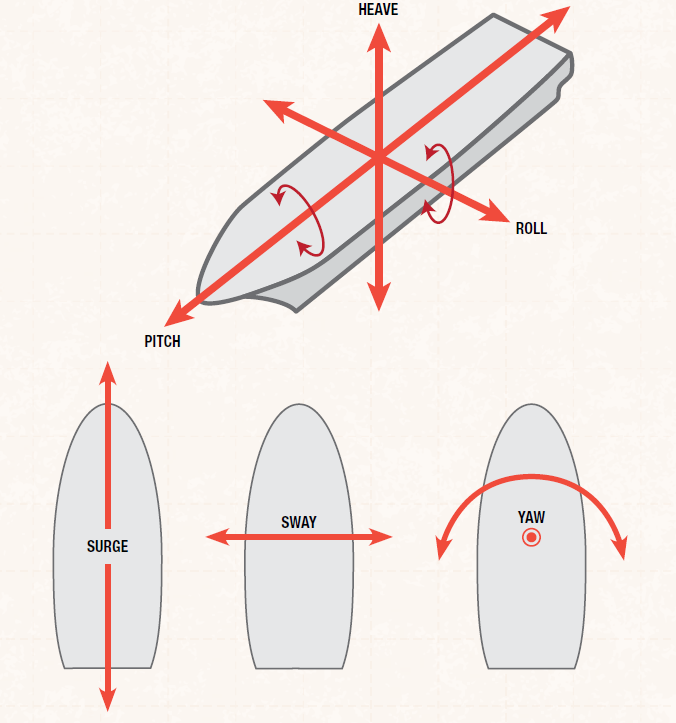
Six degrees of freedom
Any freely floating structure, including a ship, will be affected by the forces of wind, wave and current. The movements take place across two planes: the horizontal and vertical. On the horizontal plane, the vessel is subject to surge (forward and aft), sway (port and starboard) and yaw (around the horizontal axis) On the vertical plane, the vessel is subject to heave, pitch and roll. In order to maintain position, the DP system has to measure the position of the vessel, the forces acting on it and the movements of the vessel itself. It must then calculate and implement the forces necessary to counter them.
The DP system can be divided into seven components:
- Power
- Thrusters
- Environmental sensors
- Position reference sensors
- DP controller
- Hardware (generally referred to as the HMI, or human-machine interface)
- DP operator
When all components work well together, the DP systems function as one. The operator – that is, the human – is a key part of the system. To work well within it, is important to have the right training and skills – and to keep those skills updated.
Power
The power system consists of the prime mover (usually a diesel engine), alternator, cables, switchboard, bus tie breakers and power management system. DP vessels are divided into classes according to the level of redundancy that is built into their system. The higher the class of the vessel, the more complex and high-risk the tasks that it can carry out.
Thrusters
Modern-day DP vessels may be fitted with several thrusters. They may have different types of thrusters, depending upon the equipment class, design criteria and type of jobs they are engaged in. Bow and stern thrusters are usually required to turn the vessel to control its yaw movements and sway moments. These are also called tunnel thrusters, as they are fitted inside a tunnel. All types of thrusters are controlled by the DP controllers with the help of signals. The DP controller sends an ‘output signal’, also known as the ‘command signal’ to the respective thruster. Once the command is activated, the thruster sends a ‘feedback signal’ to the DP controller. Comparing the command and feedback signal is an important method to see if the thrusters are functioning well.
What’s the difference?
DP controller vs DP operator
- The DP controller is the computer which manages the system
- The DP operator is the person on the bridge
THE OPERATOR PLAYS A VITAL ROLE IN MANAGING SAFETY, AND HAS TO BE ABLE TO STEP IN IF THE SYSTEM FAILS
Environmental sensors
Environmental forces acting on the vessel make it move forward and aft, and port and starboard. These movements are measured by the position reference sensors, which then pass this information to the DP controller. In turn, the DP controller sends instructions to the thrusters to counter those movements and maintain the vessel’s position.
The three most common environmental sensors are:
-
Wind sensor: This measures the speed and direction of the wind. As the wind acts upon the ship’s side, this may result in some movement (drift). The DP system must generate an equal and opposite thrust to counter this unwanted movement.
-
Motion reference sensor: Movements in the vertical axis (roll, pitch and heave) may cause unwanted movements in the position sensors. A motion reference unit can measure all three movements so that the DP controller can counter them.
-
Gyro compass: The gyro compass measures the heading and rate of turn of the vessel. A DP class 2 vessel is expected to have three gyro compasses to ensure redundancy.
Position reference sensors
These measure the ship's position, or movement on the horizontal plane. A DP system needs to have at least one position reference sensor to automatically control surge and sway movements.
DP controller
The DP computer/controller/process station (it has various names) is a computer that takes inputs from the various environmental and position reference sensors, then gives orders to the thrusters based on the information received. This output is known as the thrust allocation logic (TAL), and has four components:
- How much thrust?
- To which thrusters?
- In which direction?
- For how long?
Hardware/HMI
The hardware used by the DP operator to control the DP system as a whole is called the human-machine interface (HMI). This includes the display, the DP control station, the joystick for manual control of the thrusters, and so on. It is important that DP operators are thoroughly familiar with the HMI – this is your workstation! The HMI must be designed to make the operator's job easy and ergonomically safe.
The operator (That’s YOU!)
Last, but certainly not least, Dynamic Positioning operators (DPOs) are appropriately qualified and experienced personnel who operate the DP system. Usually, they are deck watchkeeping officers who have graduated to be DPOs after following a recognised training scheme. DP qualification and training standards are set by The NI, in association with the DP Training and Executive Group, which is made up of representatives from major DP operators and training centres. Once the initial training has been completed, candidates must complete a set number of days of DP experience. This is an important and complex role, and qualifications have to be renewed every five years to ensure your knowledge remains up-to-date. Dynamic Positioning as a system and as a technology is here to stay, and will grow more and more important as it finds new areas and applications. It is a fascinating and rewarding way to expand your skills as a seafarer.