Free Article: A new era in maritime safety
The issues around human factors as a cause of incidents are well known in shipping. Over the years, the industry has relied heavily on administrative procedures to address these factors, but this approach has had diminishing returns. The transition from paperwork to digital formats is a start but does not solve the problem.
Captain Ian Reed
A paradigm shift in the way organisations address safety conditions and practices across vessel operations can only be achieved through a holistic approach that uses technology to create a smarter Control of Work methodology and improve the wellbeing of workers on the ground executing safety operations.
At the moment, most safety systems in shipping are paper-based. At the sharp end, the success of such systems relies on information from paper based work documentation – and on workers complying with that documentation. This information is generally only visible to the workers involved in on-site safety assessment, and can only be viewed by other stakeholders once the relevant data is retrieved and distributed more widely, such as during an audit. This limits the visibility of frontline operations in real time – and severely restricts the ability to ensure compliance and prevent incidents. Digitalised control of work processes can help by standardising the forms used across the fleet, but without connectivity, valuable information remains in its siloes.
Another issue is that seafarers’ wellbeing is not widely monitored during a voyage – even though this would offer the opportunity to inform them of unfavourable situations. For example, levels of fatigue are approximated through manually logged one-dimensional records of hours of work/rest – yet environmental and work conditions, such as intensity of physical activity and heat exposure are significant contributors to the level of readiness a seafarer has to perform tasks safely. Without active monitoring of these pre-conditions or underlying factors, initiatives and campaigns to improve crew’s health and wellbeing cannot be assessed for their effectiveness.
A lack of assurance on both procedural and human factors contributes to the risk of an incident on a vessel. It is evident that there are clear benefits to the utilisation of technology in a holistic approach to improve this situation, and improve safety all round. The Internet of Things (IOT) and Artificial Intelligence (AI) offer a number of ways to address these issues.
Human factors - the scale of the problem
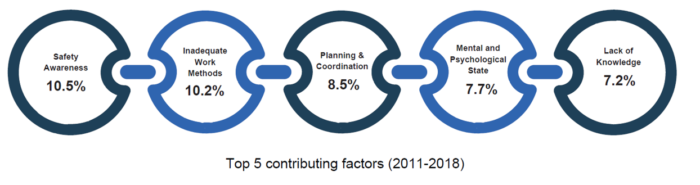
According to the European Maritime Safety Agency (EMSA) 2019 report on “Annual overview of marine casualties and incidents 2019”, 2 out of 3 of all incidents between 2011 and 2018 were contributed by human factors.
The top factors include (1) 10.5% - lack of safety awareness, (2) 10.2% - inadequate work methods, and (3) 8.5% - poor planning and coordination.
The Maritime & Coastguard Agency Marine Guidance note (MGN 520 M) summarises a wide range of contributory factors that result in maritime accidents, incidents, and errors. A consistently occurring factor is the human factor. The top three are Situational Awareness - do you know what is really happening? (22.5%), Alerting - do you really speak up when you should? (15.3%), and Communication - do you really understand each other? (13.4%)
The Oil Companies International Marine Forum (OCIMF) also issued a briefing paper in October 2020 on “The OCIMF Human Factors Approach - A framework to materially reduce marine risk”. OCIMF believes that human factors are to be adopted as i) most widely recognized; ii) addresses all individual, system, and organizational issues; iii) best supported by institutions that cater to human-centred disciplines and iv) is consistent and goes beyond International Maritime Organization (IMO) requirements associated with the human element.
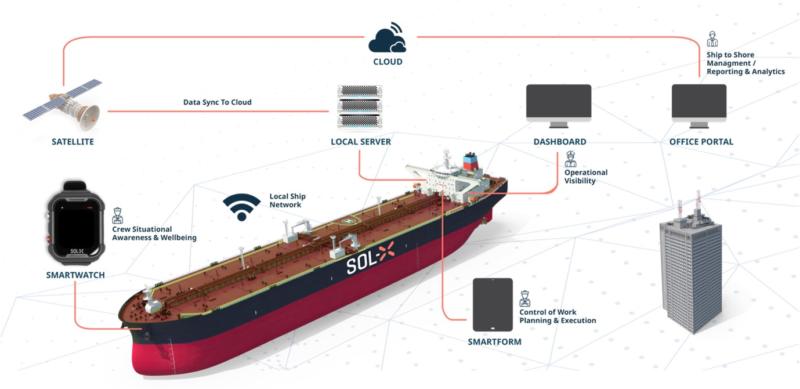
IOT to enhance end-to-end safety systems
Smart Ship/Connected Crew
Smart Ship and IOT technologies can overcome obstacles that hinder the implementation of human factor elements into organisational safety systems. A Wi-Fi enabled ship environment opens up the possibility to go beyond simple digitalisation of paperwork. It offers the possibility to create ‘intelligent’ safety workflows and improve visibility of operations and conditions of worker wellbeing. When combined with wearable IOT devices that enable contextual data capture, it is possible to increase control of the work environment, improve operational compliance and general levels of coordination between ship staff and supervisors.
This approach is known as Digitalisation of Behavioural Based Safety. A trial of this solution has been recently carried out on a gas carrier with an oil major. It has proven to be very successful and has had the full backing of the crew onboard, who have been working out ways that they can increase the functionality to improve their own safety and wellbeing.
Defined safe work behaviour
Safe work practices are implemented as intended and safety culture is promoted within the organisation
Digitalising step-by-step workflows in the form of an intelligent Permit to Work (PTW) system can help to streamline safety practices and improve compliance. When transformed into a digitalised interface in the form of a mobile tablet, these systems can automatically integrate all documentation and safety checks into a single workflow comprising:
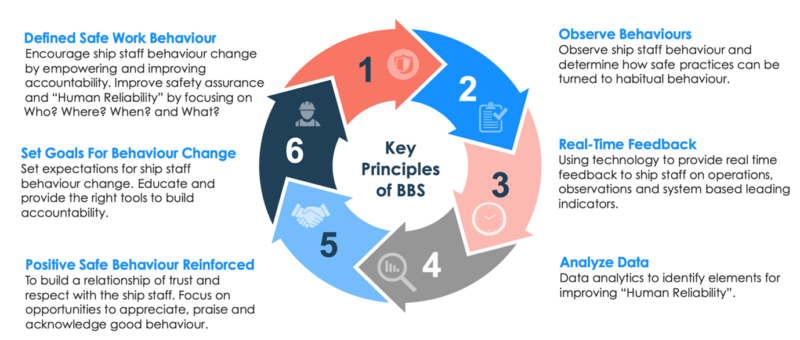
Digital Behavioural Based Safety Approach
- Risk assessments;
- Safety checklists;
- Gas readings;
- Isolation Certificate / Lock out – Tag out (LOTO) forms.
This single digital interface can be conveniently taken on-site for inspections, leading to more accurate planning and execution of tasks.
When this digital interface is linked to the officer’s wearable, it is possible to verify that the authorised officer is correctly on site when conducting critical safety workflows such as risk assessment preparation, checklist completion and gas checks. Roles and approval controls can be customised to different levels of authority for specific workflows and then verified using the wearable’s unique crew ID functionality. Overall this end-to-end digitalised workflow, supported by IOT and wearable tech, helps reduce overall risk by ensuring the right person is at the right place at the right time through better accountability.
Observe behaviours
Real time operations monitoring
A Smart Ship with an intelligent PTW system can support live information feeds that enable real time visibility of front-line operations. This is particularly important when monitoring high risk tasks and hazardous zones – critical contextual information such as location of ship staff, their identity and which jobs they are working on is now available to their supervisor in real time. This helps a supervisor manage cumulative risk. Compliance with the PTW can be ensured via remote monitoring. If crew encounter difficulties in performing their tasks or are feeling unwell, they can send an alert to the Master or responsible officers via their wearable.
Alerts can be set to monitor particular hazardous areas, such as an enclosed space entrance, alerting bridge officers to who is present in the space. The PTW will specify who is allowed to enter the space and who the standby person is. Gas readings and logs for entrants can be entered and verified in real time remotely before permission to enter is granted. Photos showing the safety equipment at the entrance to the space must be uploaded as part of the PTW process. In combination, this results in improved response, better crew communication and turnaround time on critical tasks.
Real time feedback
Situational awareness of conditions on the ground, from ship staff to shore personnel
The wearables worn by ship staff can detect and share crucial information about working conditions on the ground, hazard exposure periods and other hazards. Sensors can detect environmental exposure to heat, humidity and noise, and ship’s staff can be automatically warned to proactively take necessary precautions to avoid longer term damage. Based on this real time feedback and longer-term trend analysis, Master and Senior Officers can immediately intervene at any point to minimise risk and avoid incidents. When delivered in near real time and contextually, these interventions can prove more effective than traditional training and manual interventions.
Positive behaviour can also be reinforced through this system. For example, if ship staff are exposed to heat stress, alerts can be sent their wearable, notifying them to hydrate and to take a short break. It is easy for staff to become engrossed with their task, so these alerts help to cut through and carry out a ‘Take-Five’ safety break. Other real-time interventions include geofence alerts telling crew when they are approaching hazardous zones, so that they can take the necessary actions in advance.
The same technology can also be used in the event of an emergency resulting in a muster. Crew location can be readily seen on a control panel, highlighting the location of missing personnel. This potentially allows the early release of CO2 to the engine room if it can be seen that the missing person is in an area away from the engine room. An alert can also be sent to the Smart watch to alert crew before the release of CO2.
In addition to monitoring workflow procedures and environmental risks, wearable devices provide ship staff with real time data around their personal health and wellbeing. Sensors that provide wellbeing information such as heart rate and steps tracking can help them to better ascertain their state of fitness and readiness to work. When combined with automated systems that more accurately capture real working hours, again via wearables, crew and supervisors can more effectively balance their workloads and manage overall levels of fatigue.
Analyse data
Ensured quality of data for information is gathered from the connected wearables and digital workflows
With near instantaneous transfer of data from IOT devices such as wearables and tablets, combined with observing both the operational and environmental conditions faced by ship staff, it is now possible to accumulate large data sets that can be analysed for patterns and leading safety indicators. While it is important for onboard safety that each wearable is assigned to a specific person, all data sent for analysis is scrubbed so that it is not associated with specific users.
Personal wellbeing data points can be used to assess the efficacy of corporate wellness programs and health and safety plans. Because the data is more specific and contextual, more tailored and targeted initiatives can be developed, such as training programmes, communication campaigns and redesign of Standard Operating Procedure (SOPs).
Positive safe behaviour reinforced
Ready-made analytics and possible solutions for organisational usage
Data gathered via smart PTWs and wearables can uncover possible underlying root causes – and indicate that action needs to be taken. The following anomalies can be as seen as indicators that reflect on existing safety behaviour:
- Location mismatches: are safety checks being conducted on site?
- Missing gas readings;
- Missing sign offs;
- Incorrectly filled in Isolation Certificates/Lock out/Tag out forms.
Once documented, these indicators can then be used to encourage standardisation and sharing of best practices. In the same way, we can identify leading indicators for continuous improvements and benchmarking of high-risk activities such as entry into enclosed spaces. Organisations can then efficiently pinpoint issues that impact safety performance. Through centralisation, these safety learnings can be shared across the fleet to ensure that incidents are not repeated.
Set goals for behaviour change
Training and education
By leveraging operational and environmental data and analytics derived from connected vessels training content can specifically target those topics that are of the most concern – for example, lack of procedural compliance in specific areas.
With the aforementioned data insights, safety and compliance issues can be identified more efficiently and then addressed through proactive, targeted training and drills.
As the Energy Institute for Hearts and Minds says ‘…in order to improve safety performance, we must focus not on the person, but on the ‘environment’ the person is working in – the things leaders are saying, poor procedures, the physical environment, and various other factors.’
IOT enables and delivers a level of visibility and equips ship staff with feedback loops for continuous and longer term safety culture changes and improvement. Wearables have the potential to provide a step change in safety performance and may become a critical piece of equipment in future vessel designs with reduced crew.