202011 Improvised work aloft has bad outcome
Edited from official ATSB (Australia) report 338-MO-2018-001
A bulk carrier was in port. Following recommendations from a surveyor, the holds were to be painted to render them acceptable for grain transport. The vessel did not have any scaffolding, so it was decided to jury rig the ship’s portable gangway into a work stage. This work stage could then be suspended from the cargo crane hook via slings in order to reach the higher areas in the hold.
Company risk assessment procedures required approval from shore management for working aloft. In this case, however, approval was not sought.
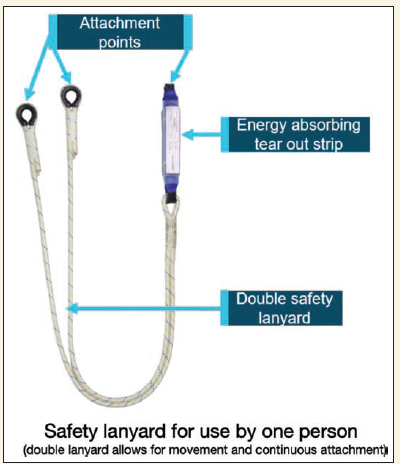
In preparation for the painting, the gangway was rigged with additional ropes to secure the open ends of the gangway. Slings were fastened either end for lifting and suspending it from the crane. Tag lines were connected to the underside of each end of the gangway and run to the hold bottom where they were to be used to control the motion of the suspended staging by two crew. Two other crew donned safety harnesses and attached themselves to the double safety lanyard on the fall arrest line – which was designed for one person – one to each attachment point.
The free end of the fall arrest safety line was tied off to one of the crane hook shackles, clear of the staging slings and the hook itself. The two ABs boarded the staging on the main deck. Because the improvised arrangement had limited stability, the ABs stood one at each end of the staging to balance it. They were to work from these positions and limit their movement so as to not upset the staging and equipment on board.
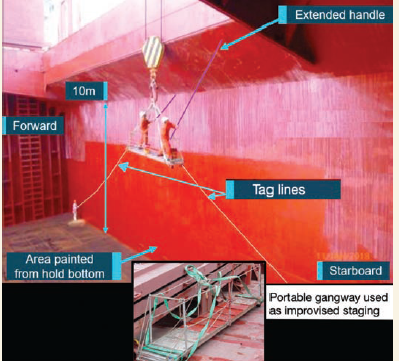
To enable the crane to reach over the hatch coaming and into the hold, the crane driver had to bypass the crane’s lower luffing limit protection. The crew members on the staging and in the hold were unaware of this – the only person who was aware was the crane driver. One of the crew on the staging signalled to the crane operator to move the hook by luffing the jib up. As the crane jib was raised, the falling block also rose and caught on the lower edge of the hatch coaming.
This went unnoticed by the work team. As the jib was raised further, the block suddenly came free of the coaming, sending an unexpected heavy shock through the staging, upsetting it and its load. Both crew were knocked over on the staging, landing heavily on their knees and lower body. The severity of their injuries meant the crew members had to be taken to hospital. The investigation found, among other things, that:
- The task was not conducted in accordance with company safety management procedures or industry best practice with regard to risk management and working aloft permit requirements. Machinery and equipment were used in a way they were not designed or approved for, making hazard identification difficult and exposing the workers to increased risk.
- The fall arrest equipment was incorrectly attached. Both workers were attached to the same device, which was designed for only one person. Had either of them fallen from the platform the equipment would not have worked correctly, resulting in serious or fatal injuries.