201948 Gas vapour detected in a ballast tank
A tanker was alongside and crew were preparing to discharge the cargo of gasoline when the fixed gas detection system alarm sounded. Hydrocarbon vapours had been detected in water ballast tank 4S. To rule out a potential malfunction of the gas detection system, ship’s staff performed the required checks with portable gas meters. These checks confirmed the presence of hydrocarbons in the tank.
The vessel was taken to anchor as a safety precaution. A contingency plan to inert the ballast tank atmosphere was prepared and approved by class and coast state authorities before it was carried out. The vessel was subsequently brought back to berth and the cargo was discharged. After discharge the vessel was re-anchored and a detailed investigation was carried out to determine why cargo vapours had entered the ballast tank.
The investigation revealed that there was a crack in the drain line of the inert gas (IG) deck seal drain line passing though ballast tank 4S. Additionally, the non-return valve was not operating correctly. At the time of loading and during topping up, the main IG isolation valve was left open after the IG system was stopped. The gases from the tank leaked back though the inoperative non-return valve, allowing cargo vapours to reach the deck seal. The ‘wet’ type deck seal performed its function by not allowing cargo vapours to pass, and the vapours were subsequently flushed out through the drain line that passed through ballast tank 4S. However, the hole in the drain line released water and cargo vapours into the ballast tank.
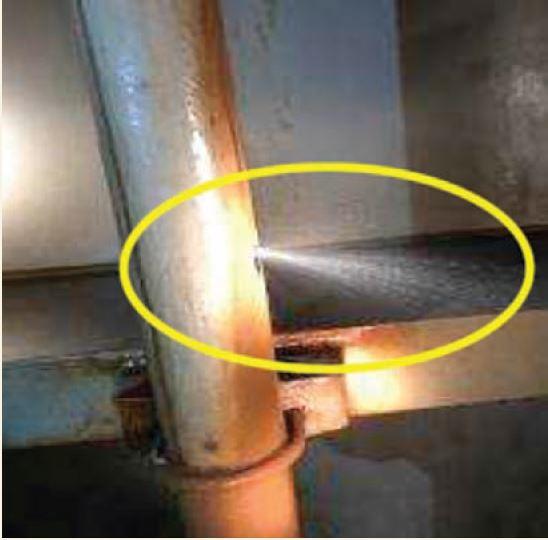
Lessons learned
- Visual inspections of IG lines and associated elements (deck seal, overboard line) may not be sufficient to detect all deficiencies. Such systems could be pressure-tested to ensure integrity.
- It should be standard practice to shut the IG isolation valve once the IG system is stopped.